Processing
PRESS BRAKE
Our in-house metal press brake bending services offer a cost-effective solution for your custom metal fabrication needs.
Features
Full 3D programming, bend visualization, and dynamic viewing during the forming process
Dynamic Thickness Compensation (DTC) to automatically compensate for variations in material thickness
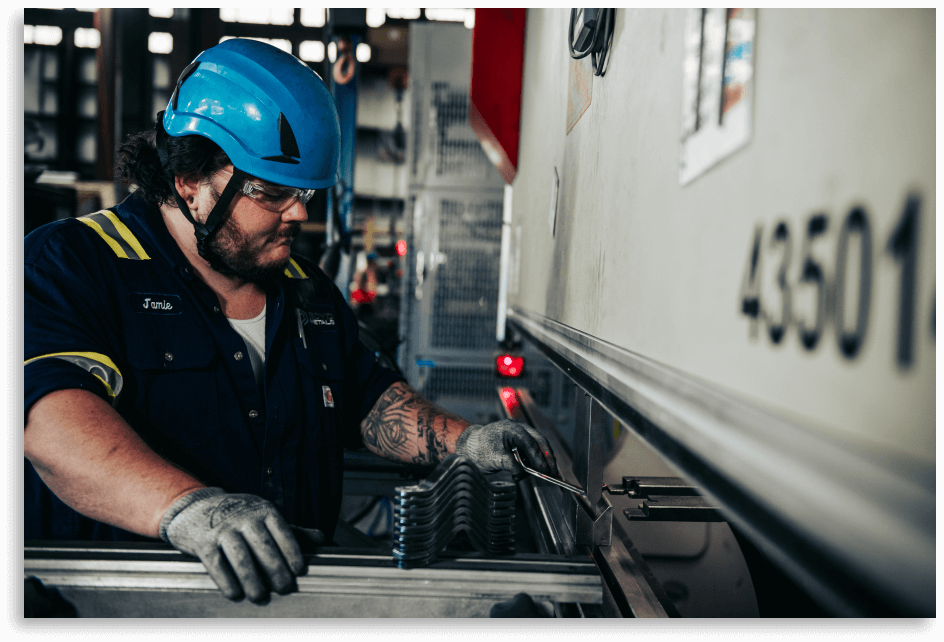
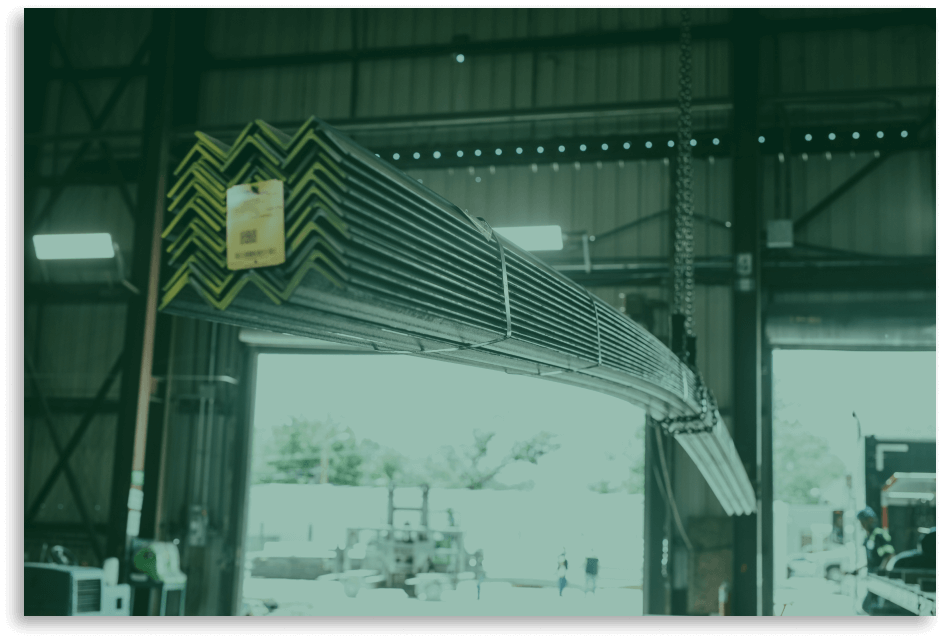
350-TON ACCURPRESS ACCELL E BRAKE
Features include:
Precision Y1/Y2 synchronized closed-loop hydraulics, allowing for repeat and parallelism positional accuracies of +/-0.0004” (0.01 mm) across the length of the metal press brake.
Vision 3D Software for full 3D programming, bend visualization, and dynamic viewing during the forming process.
Customized 16” Extended Throat Depth to facilitate parts with deeper flange lengths.
Benefits include:
Vision Control Elite Backgauge for tapered gauging applications and automatic part-gauging, offering greater flexibility in 6-axes X1/X2, R1/R2, and Z1/Z2.
Impressive ram open heights and stroke lengths to provide flexibility for complex part designs.
Frame integrity allows for precise off center bending applications.
Available at our Tyler, TX facility.
230-TON CINCINNATI PROFORM BRAKE
Features include:
Bend Simulation Software to simulate bending while displaying part, tooling, gage, bed, and ram visualization at each step to verify metal brake bending sequence and manually modify tool, part and gage positions.
Customized 16” stroke with 14’ overall bed length and 12’6” between housing.
Benefits include:
Hydraulics with dual pressure transducers for increased tonnage accuracy and digital encoders to deliver ±0.0004” (0.01 mm) ram repeatability for close-tolerance forming.
Dynamic Thickness Compensation (DTC) automatically compensates for variations in material thickness to produce the dished air bend angle for consistent parts.
Available at our Oklahoma City, OK facility.
350-TON ACCURPRESS ACCELL E BRAKE
Features include:
14” Throat Depth to facilitate parts with deep flange lengths.
Y1/Y2 machine technology allows for positional accuracies of +/-0.0004” (0.01 mm).
Wila Hydraulic Ram Clamping to suit American tooling.
Benefits include:
Impressive ram open heights and stroke lengths provide flexibility for complex part designs.
Advanced metal brake frame for precision off-center bending applications and CNC fade bends.
Available at our Joplin, MO facility.
First-Step Processing
Boyd Metals has continued to develop its metal processing capabilities with the addition of metal press brakes in its Tyler, Oklahoma City, and Joplin locations for custom metal work.